Researchers Solve Long-Standing Piezoelectric Material Challenge
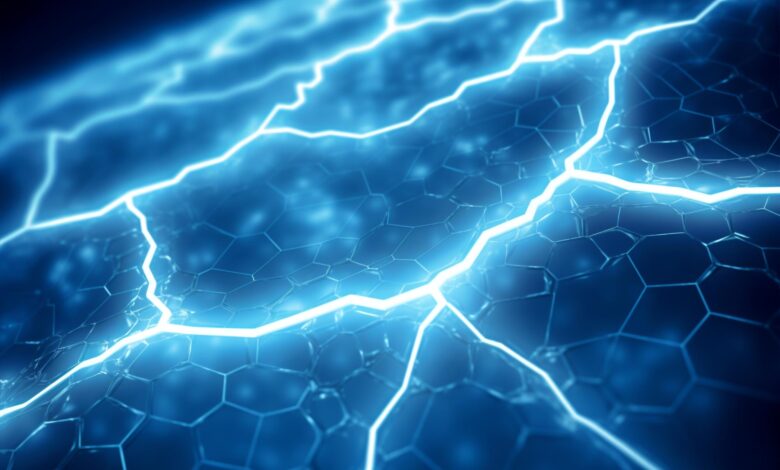
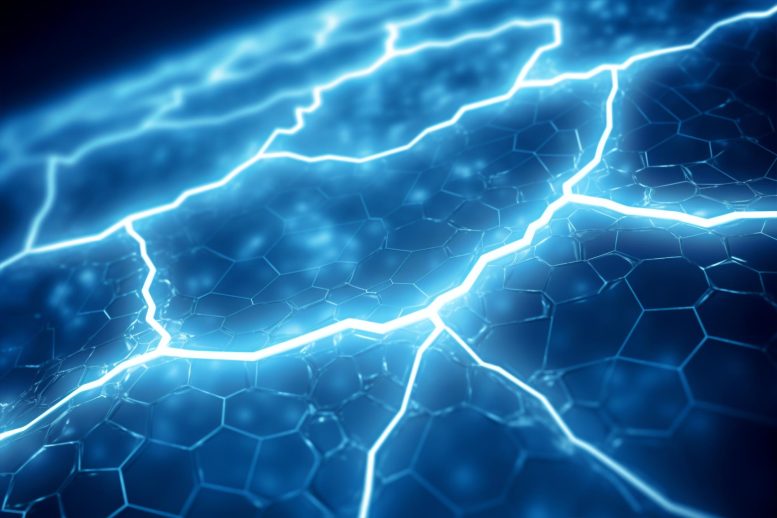
Researchers have developed a new technique that allows the restoration of piezoelectric materials used in ultrasound and sonar technologies at room temperature, simplifying repairs and enabling continuous use without the need for disassembly. This method not only enhances the durability and efficiency of these devices but also opens up possibilities for advancements in ultrasound technology. Credit: SciTechDaily.com
A new technique developed by researchers enables the restoration of crucial properties in piezoelectric materials at room temperature, streamlining repairs and extending the lifespan of ultrasound and sonar devices.
Heat and pressure can degrade the properties of piezoelectric materials essential for advanced ultrasound and sonar technologies. Traditionally, repairing this damage has involved disassembling the devices and exposing the materials to even higher temperatures. Now, researchers have developed a technique to restore these properties at room temperature, simplifying the repair process and paving the way for new ultrasound technologies.
Piezoelectric materials have many applications, including sonar technologies and devices that generate and sense ultrasound waves. But for these devices to efficiently generate sonar or ultrasound waves, the material needs to be “poled.”
That’s because the piezoelectric materials used for sonar and ultrasound applications are mostly ferroelectric. And like all ferroelectric materials, they exhibit a phenomenon called spontaneous polarization. That means they contain pairs of positively and negatively charged ions called dipoles. When a ferroelectric material is poled, that means all of its dipoles have been pulled into alignment with an external electric field. In other words, the dipoles are all oriented in the same direction, which makes their piezoelectric properties more pronounced.
Challenges in Maintaining Material Alignment
“If those dipoles aren’t in alignment it’s difficult to generate targeted ultrasound waves with the amplitude needed for them to be practical,” says Xiaoning Jiang, corresponding author of a paper on the work and Dean F. Duncan Distinguished Professor of Mechanical and Aerospace Engineering at North Carolina State University.
“Preserving the poling of piezoelectric-ferroelectric materials poses some significant challenges, because the dipoles can begin losing their alignment when exposed to elevated temperatures or high pressures,” Jiang says.
“This is also a manufacturing problem, because it limits which other materials and processes you can use when making ultrasound devices,” Jiang says. “And because the elevated temperatures aren’t even really that high – you can see alignment problems as low as 70 degrees Celsius – even shipping or storing these technologies can sometimes adversely affect the poling and the efficiency of the devices.
“What’s more, extended use of some technologies can result in the device itself generating heat that risks depoling the piezoelectric-ferroelectric material.”
And once the dipoles in the material have come out of alignment, getting them back into alignment isn’t easy. The piezoelectric-ferroelectric material needs to be removed from the device and exposed to high heat – 300 degrees Celsius or more – in order to completely depole the material before “repoling” it and pulling the dipoles back into alignment.
“It’s important to re-use these piezoelectric-ferroelectric materials because they are usually expensive – you don’t want to just throw them away,” Jiang says. “But often the material is retrieved and the rest of the ultrasound device is discarded.
“We have developed a technique that allows us to depole and repole piezoelectric-ferroelectric materials at room temperature. That means we can pull the dipoles back into alignment without removing the material from the device – and this can be done repeatedly, as needed.”
Understanding the New Technique
To understand the new technique, you need to understand that there are two ways to pull the dipoles in a piezoelectric-ferroelectric material into alignment. The most widely used technique involves applying a direct current (DC) electric field to the material, which pulls all of the dipoles in the same direction.
“This way works well for creating alignment, but it is virtually impossible to depole the material using only a DC field,” Jiang said.
The other technique involves applying an alternating current (AC) electric field to the material, which causes the dipoles to oscillate in response to the waves in the field, until the field is removed, at which point the dipoles lock into place in alignment.
“We found that we can also depole the material using an AC field, even at room temperature. If the material was originally poled using a DC field, we could remove much of the poling with an AC field – but not all of it,” Jiang said. “However, if the material was originally poled with an AC field, we found that could also completely depole the material using an AC field.”
The finding has at least two significant ramifications for ultrasound technologies.
“If we can pole piezoelectric-ferroelectric materials at room temperature, it means we can alter the other materials and manufacturing processes we use when creating ultrasound devices to optimize their performance,” Jiang says. “We are no longer limited to materials and processes that won’t affect the polarization in the piezoelectric-ferroelectric components, because we can pole the material using an AC field after the device has been assembled.
“What’s more, it means that we can easily repole the materials in existing devices, hopefully giving us a long lifetime of peak performance for these technologies.”
Reference: “Electrical de-poling and re-poling of relaxor-PbTiO3 piezoelectric single crystals without heat treatment” by Hwang-Pill Kim, Mao-Hua Zhang, Bo Wang, Huaiyu Wu, Zhengze Xu, Sipan Liu, Sunho Moon, Yohachi Yamashita, Jong Eun Ryu, Jun Liu, Shujun Zhang, Long-Qing Chen and Xiaoning Jiang, 30 July 2024, Nature Communications.
DOI: 10.1038/s41467-024-50847-3
This work was done with support from the Office of Naval Research, under grant N00014-21-1-2058; the National Science Foundation, under grants 2011978, 2309184 and 2133373; and from the U.S. Department of Energy’s Lawrence Livermore National Laboratory under contract DE-AC52-07NA27344.