Backed by tech and innovation, ‘Made in Hong Kong’ is coming back stronger than ever
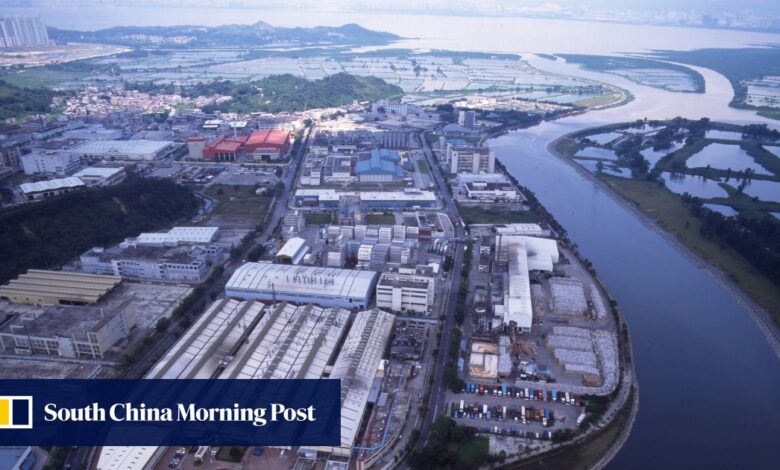
In the 1950s and 60s, entrepreneurs tapped a fast-growing supply of manpower to turn Hong Kong into a global manufacturing and export hub. The city specialised in high-volume production for companies worldwide, churning out products including garments, plastic goods, toys and electronics.
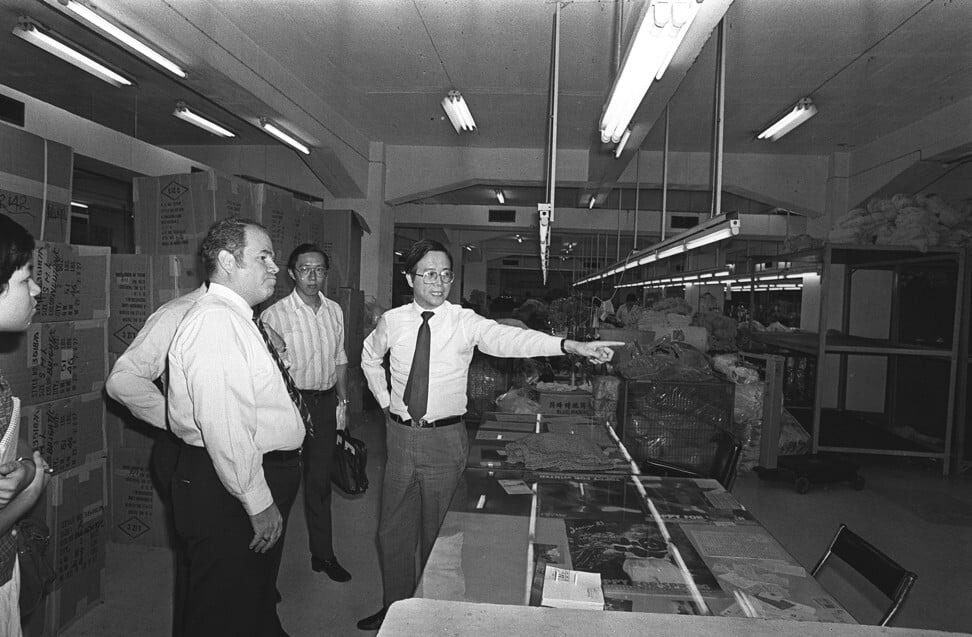
But as Hong Kong’s economy matured in the late 1970s and early 80s, it began to place more emphasis on the services sector, and manufacturers relocated their factories north of the border to take advantage of more affordable labour and land in mainland China.
Someone who has witnessed the city’s industrial evolution firsthand is Dr Alex Wong Siu-wah, the founder and CEO of King’s Flair, a long-established kitchenware manufacturer. He started working in a Hong Kong factory after graduating high school, while also taking evening courses in mechanical and electronic engineering. But Wong was keen to work on his own ideas, so in 1979 he started his own business.
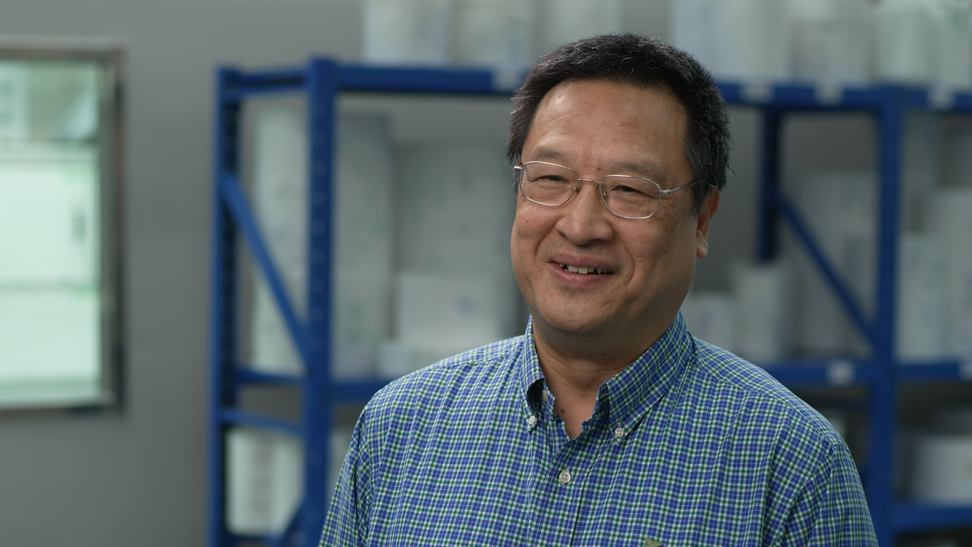
Fast-forward to today, and Wong holds an honorary doctorate of business from Swinburne University of Technology in Melbourne, awarded in 2018, in addition to a doctorate of business administration from Hong Kong Polytechnic University that he completed in 2019.
Meanwhile, King’s Flair has come to specialise in OEM (original equipment manufacturing) as well as ODM (original design manufacturing), providing end-to-end services for international household brands that see products through from concept to consumer. The company prides itself on innovation and maintaining a competitive edge in a fast-changing market, which has led it to adopt advanced manufacturing.
From Wong’s experience, advanced manufacturing goes beyond automation. “One of the core values of advanced manufacturing is sustainability. This means you need to know how to use new technology to sustain your company,” he says. “You also have to think about product design, production ideas, marketing. These factors are all related to the data collection that feeds into the computer usage for advanced manufacturing.”
New era in manufacturing
“[Hong Kong] used to be one of the ‘Four Little Dragons’ of Asia – we used to do a lot of manufacturing,” says Albert Wong, CEO of Hong Kong Science and Technology Parks Corporation (HKSTP). “At the moment, industry occupies less than 1 per cent of the GDP. In other economies, [it’s] 20 or 30 per cent. We need diversity in our economy.”
Nearly half a century on, manufacturing has transformed thanks to big leaps in technology. There is now demand for high-quality design and customisation, while the focus has shifted to increasing value instead of simply lowering costs. These trends open a path for manufacturing to come back to Hong Kong as part of the city’s ongoing pursuit of innovation.
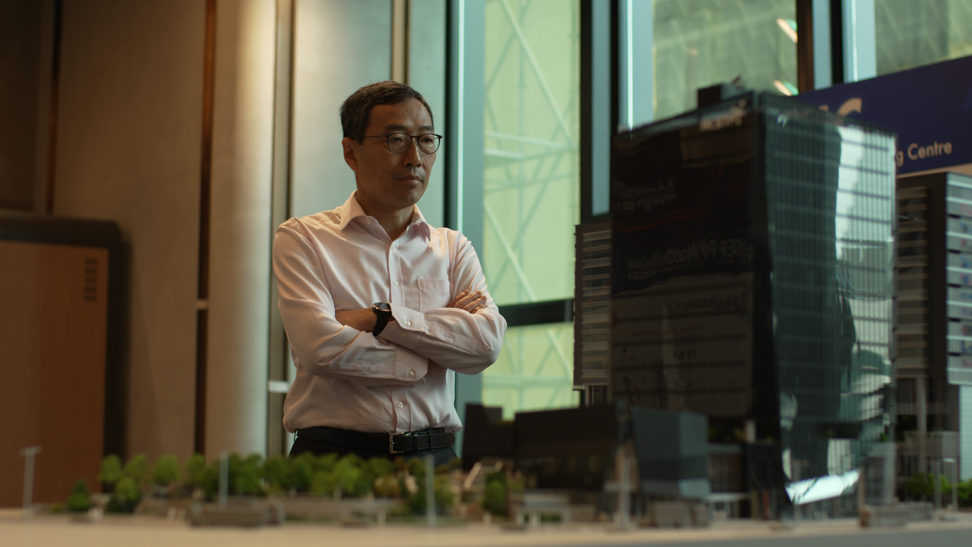
“We cannot bring back the old, labour-intensive manufacturing, but we need to bring back its future,” Wong says. “That means high-end manufacturing, advanced manufacturing, automation or a lot of digital support. This will generate a wealth of new business opportunities, high-skilled employment and a promising future for the young generation as well.”
There is more to advanced manufacturing than “Industry 4.0”, the phrase that some use when referring to the concept. Advanced manufacturing involves applying technology solutions to improve production, thereby achieving “better performance, better products and much better customisation”, according to Dr H.L. Yiu, HKSTP’s head of reindustrialisation.
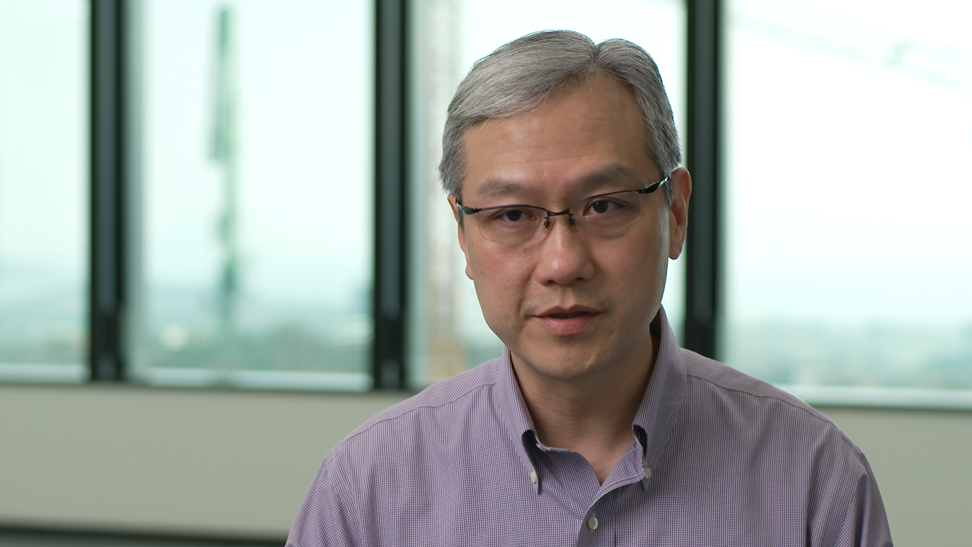
This allows the “Made in Hong Kong” label to mean much more than it did in the past. “If you have an idea, you can design and develop it in Hong Kong, and even have it made in Hong Kong,” Yiu adds. “The value of the product can be made much higher than if you merely make it in Hong Kong, because innovation brings life to the product.”
Reinforcing Hong Kong pride through reindustrialisation
HKSTP’s reindustrialisation effort aims to create a new economic growth engine for Hong Kong by using I&T to help companies and start-ups turn their research into products, while also supporting established manufacturers in adopting new technologies to upgrade and transform their businesses.
In Tseung Kwan O, HKSTP is constructing the Advanced Manufacturing Centre (AMC) to empower local companies looking to tap into this new era of reindustrialisation. The multi-storey facility is a purpose-built space in which to install advanced manufacturing operations. It will have a floor area spanning 1.1 million square feet, higher ceilings, anti-vibration floors to support heavily vibrating machinery, and communal warehouse and logistics areas, in addition to a Proshop that helps tech companies take prototypes into production.
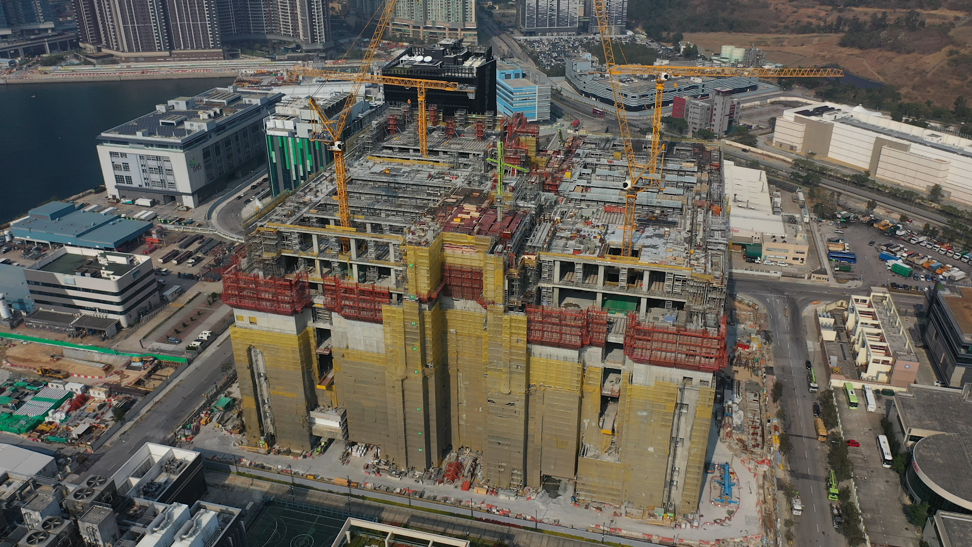
Slated for completion in 2022, the AMC project is part of HKSTP’s ongoing revitalisation of industrial estates in Tai Po, Yuen Long and Tseung Kwan O into bases for advanced manufacturing. “This will make ‘Made in Hong Kong’ even stronger in the future, for much better product design, reliability, safety and quality,” Yiu says.
Hong Kong-made products have long been received with high confidence by consumers around the world. Both Albert Wong and Yiu believe that reindustrialisation and advanced manufacturing – supported by the city’s reputable testing and certification ecosystem with comprehensive quality control – will further elevate the “Made in Hong Kong” label as both a global standard and source of local pride.
From kitchenware to nanofibre
King’s Flair is one of the Hong Kong enterprises that is set to move into AMC, as part of the company’s efforts to diversify through new technologies. After King’s Flair went public in 2015, Alex Wong set up a subsidiary called Nanoshields Technology to explore uses of nanotechnology in household products, such as air and water filtering.
“We worked with a university and found that nanofibre is a very good material for filtration,” he says. Wong also collaborated with the Nano and Advanced Materials Institute (NAMI), a research and development centre in Hong Kong, to develop a more effective filtering technology with the advanced material for commercialisation.
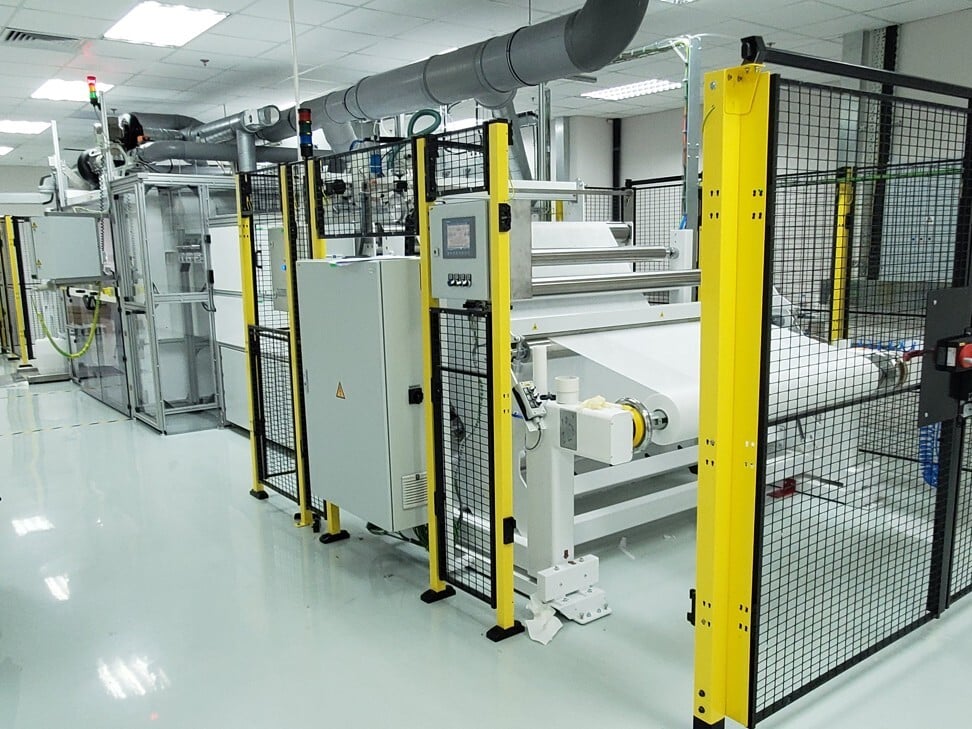
In 2018, Nanoshields acquired four separately operated production lines to make its own nanofibre. That advanced manufacturing equipment will be moved to AMC, after HKSTP consulted with Nanoshields to ensure the facility will meet required specifications. “For instance, we need a special warehouse for our chemicals,” Wong says. “We expect our workshop at AMC to completely meet our strict requirements for temperature and moisture control.”
AMC will become a key driver of reindustrialisation in Hong Kong, connecting the manufacturing industries and HKSTP’s I&T ecosystem, which includes 1,000 tech companies and strong R&D capabilities developed over almost 20 years.
“In order to make reindustrialisation work in Hong Kong, you need to have the ecosystem with different stakeholders,” Albert Wong says. “We have the government support right there. We need the research and the universities to bring in the technologies. We need the talent. And we need the industrialists, infrastructure, the market and the investment.
“We have all the elements, we just need to … get them to work together.”
Source link