NASA Unveils Game-Changing Augmented Reality in Spacecraft Engineering
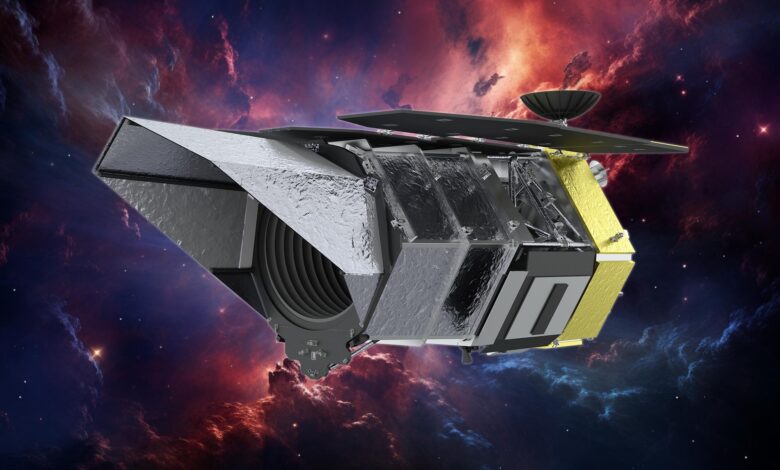
By
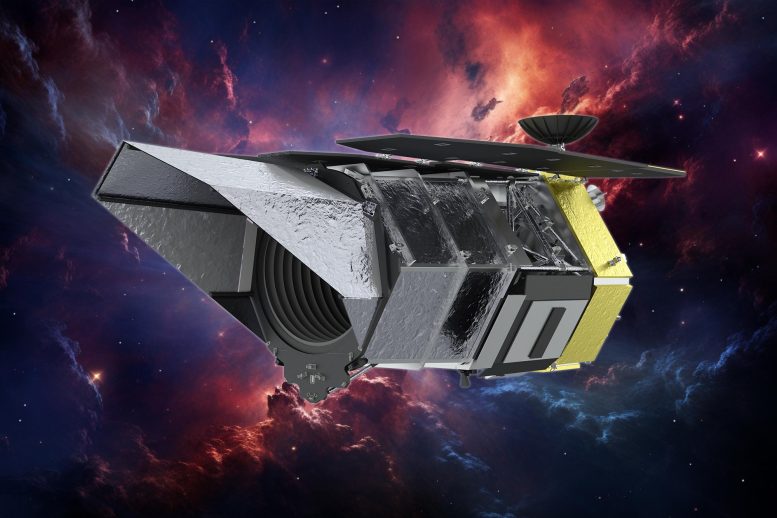
NASA technicians at the Goddard Space Flight Center are using advanced AR headsets and other technologies to enhance the assembly process of the Roman Space Telescope. This method allows precise alignment of parts, saving time and reducing costs. The integration of AR, QR codes, and robotics not only streamlines construction but also facilitates remote collaboration and improves accuracy in installations. Credit: NASA’s Goddard Space Flight Center
At NASA’s Goddard Space Flight Center, AR technology and robotics are revolutionizing the assembly of the Roman Space Telescope by enhancing precision and efficiency, leading to significant time and cost savings during construction.
- Augmented reality tools have helped technicians improve accuracy and save time on fit checks for the Roman Space Telescope being assembled at NASA’s Goddard Space Flight Center in Greenbelt, Maryland.
- In one instance, manipulating a digital model of Roman’s propulsion system into the real telescope structure revealed the planned design would not fit around existing wiring. The finding helped avoid a need to rebuild any components.
- The R&D team at Goddard working on this AR project suggests broader adoption in the future could potentially save weeks of construction time and hundreds of thousands of dollars.
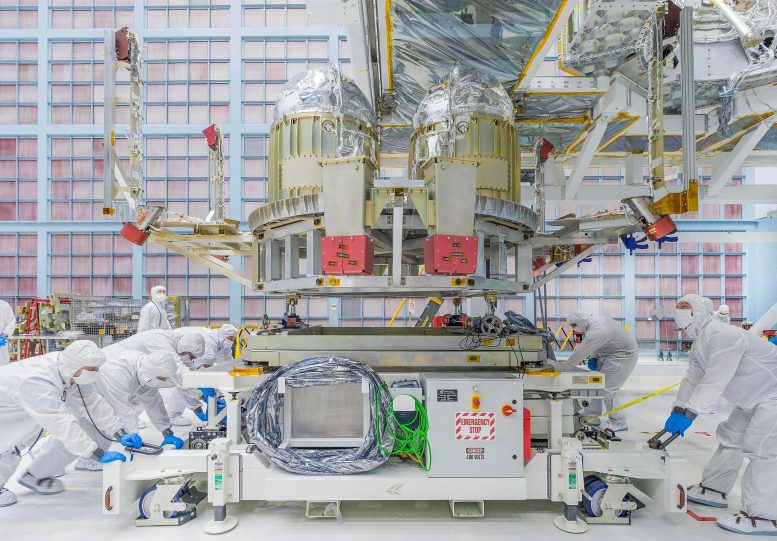
In this photograph from February 29, 2024, at NASA’s Goddard Space Flight Center in Greenbelt, Md., the Roman Space Telescope’s propulsion system is positioned by engineers and technicians under the spacecraft bus. Engineers used augmented reality tools to prepare for the assembly. Credit: NASA/Chris Gunn
Innovative Spacecraft Assembly Techniques
Technicians armed with advanced measuring equipment, augmented reality headsets, and QR codes virtually checked the fit of some Roman Space Telescope structures before building or moving them through facilities at NASA’s Goddard Space Flight Center in Greenbelt, Maryland.
“We’ve been able to place sensors, mounting interfaces, and other spacecraft hardware in 3D space faster and more accurately than previous techniques,” said NASA Goddard engineer Ron Glenn. “That could be a huge benefit to any program’s cost and schedule.”
Projecting digital models onto the real world allows the technicians to align parts and look for potential interference among them. The AR heads-up display also enables precise positioning of flight hardware for assembly with accuracy down to thousandths of an inch.
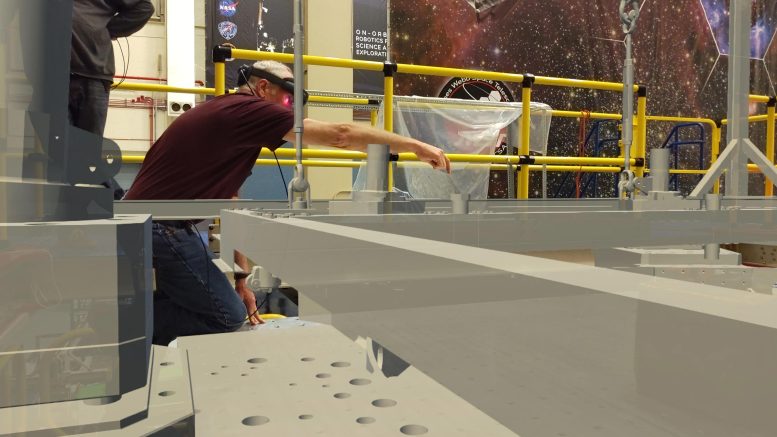
Engineers wearing augmented reality headsets test the placement of a scaffolding design before it is built to ensure accurate fit in the largest clean room at NASA’s Goddard Space Flight Center in Greenbelt, Md. Credit: NASA
Advancements in Augmented Reality for Spacecraft
Using NASA’s Internal Research and Development program, Glenn said his team keeps finding new ways to improve how NASA builds spacecraft with AR technology in a project aiding Roman’s construction at NASA Goddard.
Glenn said the team has achieved far more than they originally sought to prove. “The original project goal was to develop enhanced assembly solutions utilizing AR and find out if we could eliminate costly fabrication time,” he said. “We found the team could do so much more.”
Enhancing Efficiency with AR and Robotics
For instance, engineers using a robotic arm for precision measuring and 3D laser scanning mapped Roman’s complex wiring harness and the volume within the spacecraft structure.
“Manipulating the virtual model of Roman’s propulsion assembly into that frame, we found places where it interfered with the existing wiring harness, team engineer Eric Brune said. “Adjusting the propulsion assembly before building it allowed the mission to avoid costly and time-consuming delays.”
Roman’s propulsion system was successfully integrated earlier this year.
Considering the time it takes to design, build, move, redesign, and rebuild, Brune added, their work saved many workdays by multiple engineers and technicians.
“We have identified many additional benefits to these combinations of technologies,” team engineer Aaron Sanford said. “Partners at other locations can collaborate directly through the technicians’ point of view. Using QR codes for metadata storage and document transfer adds another layer of efficiency, enabling quick access to relevant information right at your fingertips. Developing AR techniques for reverse engineering and advanced structures opens many possibilities such as training and documentation.”
The Roman Space Telescope is a NASA mission designed to explore dark energy, exoplanets, and infrared astrophysics.
Equipped with a powerful telescope and advanced instruments, it aims to unravel mysteries of the universe and expand our understanding of cosmic phenomena. Roman is scheduled to launch by May 2027. Credit: NASA’s Goddard Space Flight Center
Future Applications and Cost Savings
The technologies allow 3D designs of parts and assemblies to be shared or virtually handed off from remote locations. They also enable dry runs of moving and installing structures as well as help capture precise measurements after parts are built to compare to their designs.
Adding a precision laser tracker to the mix can also eliminate the need to create elaborate physical templates to ensure components are accurately mounted in precise positions and orientations, Sanford said. Even details such as whether a technician can physically extend an arm inside a structure to turn a bolt or manipulate a part can be worked out in augmented reality before construction.
During construction, an engineer wearing a headset can reference vital information, like the torque specifications for individual bolts, using a hand gesture. In fact, the engineer could achieve this without having to pause and find the information on another device or in paper documents.
In the future, the team hopes to help integrate various components, conduct inspections, and document final construction. Sanford said, “it’s a cultural shift. It takes time to adopt these new tools.”
“It will help us rapidly produce spacecraft and instruments, saving weeks and potentially hundreds of thousands of dollars,” Glenn said. “That allows us to return resources to the agency to develop new missions.”
This project is part of NASA’s Center Innovation Fund portfolio for fiscal year 2024 at Goddard. The Center Innovation Fund, within the agency’s Space Technology Mission Directorate, stimulates and encourages creativity and innovation at NASA centers while addressing the technology needs of NASA and the nation.